CO2 to ethylene glycol, a major breakthrough!
2024-08-02
Ethylene glycol is currently produced by an energy-intensive two-step thermo-catalytic process
First Author: FAN LeiCorrespondence Author: Wang Lei Correspondence Unit: National University of Singapore
Ethylene glycol is currently produced through an energy-intensive two-step thermal catalytic process, which results in a large numberCO2emissions. ByElectrooxidation of ethylene powered by renewable electricity Sustainable ethylene glycol productionis desirable; however, the direct electro-oxidation of ethylene has unsatisfactory product selectivity, particularly at high productivities. Here, the authors report a cascade strategy for the efficient and selective production of pure ethylene glycol solutions under ambient conditions without detectable by-product formation. Specifically, the use of electrochemically generated hydrogen peroxide as an oxidant, in the catalyst./The solid acid complex converts ethylene to ethylene glycol. Using an integrated solid electrolyte reactor, the authors have worked on industrially relevant current densities (100-500 mA cm.2)realized60-70%High electron utilization efficiency, Used in ethylene glycol production, with complete product selectivity (~100%). The authors further relate the systemCO2Electro-reduction reactor integration, anddemonstrated the useCO2Sustainable production of pure ethylene glycol with water as the only raw material.Article“Selective production of ethylene glycol at high rate via cascade catalysis”for the title,2023Year6Month26Day published inNature CatalysisJournal.research background1. Ethylene glycol is widely used as a polyester fiber precursor, antifreeze, coolant and energy carrier.2020Year, GlobalEthylene glycol production over4000million tonsIt is expected to grow annually.5-10%, broad application prospects.2. At present, ethylene glycol is produced by a two-step method with high energy consumption and has a large numberCO2emissions and other waste streams. In this method, ethylene is first oxygen on a silver-based catalyst (O2) Oxidation to form ethylene oxide, and then strong acid catalyzes the hydrolysis of ethylene oxide to ethylene glycol. due to the unavoidable over-oxidation of ethylene in the first step,The total product selectivity of the process is lower80%. In addition, several separation steps must be integrated into the process to provide the final product, thus.added more cost.3. With the rapid development of renewable energy generation, electrified chemical manufacturing provides a sustainable way for chemical production under environmental conditions.Recently, palladium-based electrocatalysts for the electrochemical oxidation of ethylene to ethylene glycol in aqueous electrolytes have been explored. By optimizing the binding energy of the hydroxyl intermediate on the palladium surface, an increase in the selectivity of ethylene glycol formation was observed, although the current density was moderate (~5 mA cm.-2). When a higher current is applied, non-negligible ethylene peroxidation and by-product formation occur (I. e.>20%The combined selectivity of glycol aldehyde, acetaldehyde, ethylene oxide, formic acid andCO2). In general, in addition to the precious metals used,These selectivity challenges still hinder the practical implementation of direct electro-oxidation of ethylene towards sustainable ethylene glycol production.4. In order to circumvent the above limitations of thermal catalysis and direct electrochemical ethylene oxidation,The authors developed a cascade catalytic method to achieve selective production of pure ethylene glycol solutions at industrially relevant current densities under ambient conditions. The first step in the cascade process is an electrocatalytic process; the second step is a thermal (heterogeneous) catalytic process. as shown in Fig. In Fig.1cfirst constructed to be able to produce a separation from any ionic electrolyteH2O2Electrochemical reactor for pure flow of solution. The reactor uses a two-electron oxygen reduction reaction (2e-ORR) exhibit high Faraday efficiency (FE)(>90%) And adjustable current density. Compared with the energy-intensive anthraquinone process, this strategy has been proven to have the advantages of low energy consumption, modularity and on-demand production, avoiding the needH2O2storage and transport needs. In the subsequent reactor, the authors used a heterogeneous catalyst (titanium silicalite-1(TS-1)) and solid acids (sulfonated polystyrene-divinylbenzene), on which it can be approximately100%The product selectivity of is to form ethylene glycol directly as a pure stream.The author's design successfully decoupled ethylene oxidation and electrode potential, thereby not only avoiding the inevitable ethylene peroxidation, but also simplifying the reactor design and downstream product separation/Purification. Achieve high electron glycol efficiency (ETE;method) in the industry-related current density (100-500 mA cm.-2) for the production of ethylene glycol.60-70%yield, and provide up5.31mmol h-1high ethylene glycol production rate. The authors further relate the system to electrochemicalCO2reduction reactor coupling to achieve a reduction fromCO2Production of ethylene glycol. Based on preliminary technical and economic analysis,The authors demonstrate that their strategy can achieve sustainable ethylene glycol production with good economic feasibility and negative CO2 emissions.
Figure1 Schematic comparison of ethylene glycol production pathways
Introduction of results
Decoupling of ethylene oxidation by cascade catalysis
Control of electrochemical reactions involving carbon (such as direct ethylene electrooxidation and electrochemicalCO2reduction) the main challenge of selectivity stems from the multifunctional bonding properties of carbon atoms. Thus, these reactions often involve complex reaction networks/intermediate, its counter electrode-Changes in the chemical state, composition, facet and morphology of the electrolyte interface and the electrode potential, localpHand highly sensitive to quality transmission. Therefore, it is often difficult to control the selectivity of these reactions and to produce the desired product in high yield. Thus, avoiding undesirable ethylene peroxidation and by-product formation is challenging, especially when the overpotential is increased to achieve high production rates. In order to solve this problem,The authors' strategy is to decouple the ethylene oxidation step from the high-energy electrode surface while still using an electrochemically generated oxidizing reagent to oxidize ethylene.The author first determinesH2O2As a good candidate, the author aims, from an energy and environmental point of view. Specifically,H2O2has a sufficient standard reduction potential to oxidize ethylene and can be oxidized2e−ORRElectrochemically obtained. The authors measuredETEand productivity. In10 mA cm.2When the ethylene glycol is the maximumETEAbout66%, andETEdecreased slightly with the increase of the applied current density, which may be dueH2O2Accumulation at high current densities leads to aH2O2Excessive reductionH2O. On the other hand, the ethylene glycol production rate first increases with the current density, and in30 mA cm.-2When the maximum value is reached0.23 mmol h-1and then at even higher50 mA cm.-2The current density is slightly reduced. The reduced ethylene glycol production rate at high current densities may be dueH2O2Electrochemical decomposition at high overpotential.
Figure2 Production of ethylene glycol by cascade catalysis
The Importance of Using Acidic Electrolytes
It has been previously observed that ethylene oxide isTS-1Catalyzed ethylene oxidation is the main product, and an additional hydrolysis step is required to provide ethylene glycol as the main end product. To address this challenge, the authors conducted preliminary tests prior to cascade catalysis, in whichTS-1Added to a continuous ethylene purge.1000 ppm H2O2in solution. Reaction1Hours later, the author passed1H NMRThe resulting solution was measured and a mixture of ethylene oxide and ethylene glycol was observed.Product ratio of ethylene glycol to ethylene oxide up1:2.5. Previous work has shown that,TS-1Catalytic passage of ethylene throughH2O2oxidation, firstC = CThe epoxidation of the bond forms ethylene oxide, which is then used inTS-1of acidic sites (including acid formsTi-OOHand the Lewis acid site of the framework titanium substance) on hydration to give the final product ethylene glycol.Therefore, the authors speculate that acidic conditions may be beneficial inTS-1on the formation of ethylene glycol. To test this, the authors then added to the above solution0.1M H2SO4to increase the selectivity of ethylene glycol. The results proved to be positive; the ethylene glycol1HNMRThe peak intensity increases significantly at the expense of the disappearance of the ethylene oxide peak. Based on these observations, the authors willH2SO4incorporated into the electrolyte to promote overall selectivity to ethylene glycol. As a result, ethylene glycol was the only product observed in the authors' system. In other words, complete product specificity for direct ethylene oxidation to ethylene glycol is obtained, which does not appear to have been achieved before.
Figure3 Study on the mechanism of cascade catalytic system
H2O2Kinetic matching of production and utilization
Due toThe high product specificity of ethylene glycol in the authors' system, the total of the final productETEByH2O2formedFEandH2O2utilization efficiency decision. AlthoughH2O2ofFEremained high at all current densities (90%), but the overall Eter is lower and decreases along the increase of the total current density.H2O2FEandETEThis mismatch betweenTS-1limited catalytic activity for the oxidation of ethylene, or otherH2O2The existence of decomposition pathways. Regarding the second reactor, when the authors simply put the solid electrolyteH2O2When the production reactor is integrated with an ethylene oxidation reactor, the main product is ethylene oxide rather than ethylene glycol, similar to what the authors have previously observed. Because the author uses pureH2O2production of solid electrolytes (sulfonated polystyrene-divinylbenzene) is also highly acidic, and the authors hypothesize that the same solid electrolyte can also promote direct ethylene glycol formation, similarH2SO4The function.Therefore, the authors directly relate the solid acid electrolyteTS-1mixed, and the solid acid/The catalyst composite is introduced into an ethylene oxidation reactor. As expected, a pure ethylene glycol stream was successfully obtained by cascade catalysis.Under optimized conditions, at all test current densities (10-200 mA cm.2),ETEcan reach about70%. The production rate of ethylene glycol increases with the increase of current density, and the maximum value is2.4 mmol h− 1, in electrolysis1After about an hour.0.08MThe final product concentration of (Fig.4 e). In addition, the ethylene glycol production rate is related toH2O2The production rate increases proportionally with a slope0.75, as shown in4fshown, indicating75%Electrochemically generatedH2O2It has been used for ethylene glycol production. MissingH2O2probablyTS-1induced decomposition, which the authors believe can be largely circumvented by designing catalysts with kinetics that favor the oxidation of ethylene.
Figure4 Cascade Production of Pure Ethylene Glycol Solution
Increasing ethylene glycol productivity
In order to further improve the catalytic performance, the authors screened several different functional groups based onCNTmaterials, and the amine-functionalizedCNT(Cnt-hr 2 camera) are identified in the author's solid electrolyte reactorH2O2Produces the most effective electrocatalysts. Under typical conditions,Cnt-hr 2 cameraIn2.05VThe relatively low battery voltage isH2O2Production provided500 mA cm.2The high current density of (Fig.5a). The maximum ethylene glycol production rate reaches5.3 mmol h-1(Fig.5 b,c), when appliedH2O2Produced500 mA cm.-2high current density. Due to the retentionH2O2formation and subsequent selectivity of ethylene glycol production, the total electron utilization efficiency of ethylene glycol production remains> 60%The high level. in addition,The authors achieved a high current density (200 mA cm.-2) under the continuous production of pure ethylene glycol flow over24hours, and has a fairly stableETEand battery voltage (Fig.5d). By scaling up the electrochemical reactor4cm2and reduce the water flow rate, the authors canProduces a high concentration of ethylene glycol solution, up0.5M(Fig.5e)。Overall, the authorSuccessfully demonstrated that a cascade system can be used to produce a pure ethylene glycol stream at a practical production rate, And the author believes that due to its simple and effective design, it is feasible to expand the author's system.
Ethylene oxidation at the cathode and anode
In order to prove the adaptability of the author's system, the author designed and integrated a three-chamber reactor, and realized that ethylene oxidation was carried out simultaneously at the anode and cathode. as shown in Fig. As Shown5fAs shown, independent production of ethylene glycol and ethylene oxide is achieved on both sides of the electrical reactor.The electron utilization efficiency of ethylene glycol and ethylene oxide production is achieved simultaneously at all current densities applied60-70%(100-300 mA cm.-2, as shown in1bshown). Corresponding battery voltage in Supplementary Fig.5g)。A detailed discussion and techno-economic analysis of the design of this integrated reactor further confirm the promising potential of the author's cascade strategy for the production of ethylene glycol.
Figure5 Catalyst and system optimization for more practical applications
ByCO2Production of ethylene glycol
In Fig.6aIn, the authors first adopted a solid electrolyte-basedCO2The electro-reduction reactor produces ethylene, which is then sent to the cascade reactor described above for ethylene glycol production.ForCO2electroreduction, useCu2ONanocubes (100 nm) as a catalyst precursor. In200 mA cm.2When the maximum ethyleneFEFor48%. other liquid products, including ethanol, acetic acid, formic acid and n-propanol, while producing totalFEApproaching28%.To achieve the relevant ethylene production rates, the authors used dimensions4cm2of the cathode to maintain800 mA(200 mA cm.-2) of the high totalCO2reduction current. Then, the author will export gas (CO2,C2H4,COandH2mixture) directly to the ethylene oxidation reactor without purification. In100 mA(1 cm2,100 mA cm.-2), the production rate of ethylene glycol is only0.2 mmol h-1, corresponding12%ofETE. UnsatisfactoryETEThis may be due to the low ethylene concentration in the outlet gas mixture. To test this, the authors then introduce concentratedKOHsolution to remove excess gas mixtureCO2so that the ethylene concentration can be significantly increased. As expected,The production rate of ethylene glycol increased to approx.0.5 mmol h-1, and for glycol production, the correspondingETEalso doubled. Therefore, the authors believe that further optimization of the kinetic match between ethylene production and oxidation can leadCO2Even higher overall current efficiency for the production of ethylene glycol.
Figure6 FromCO2Cascade production of ethylene glycol
Full text summary
developed a cascade catalytic system, which involves electrocatalysis and then thermal catalysis to produce ethylene glycol. The integrated system shows complete product selectivity under mild conditions.using electrochemically generatedH2O2As an oxidant and abundant titanium silicate as a catalyst, the high totalETEof~70%The production of ethylene glycol is realized.First, when compared with solid electrolyte-basedH2O2generating reactors when combined, the authors maintain a highETEAt the same time, the practical current density (I. e,500 mA cm.-2) under ethylene glycol production.Secondly, due to the combination of catalyst and solid acid, a pure ethylene glycol stream is obtained, which promotes the separation of downstream products/Purification. And finally,Cascade systems have been shown up100Hours of continuous glycol production for excellent durability. The authors also designed the useCO2An integrated system for the production of ethylene glycol, which replaces fossil fuel-derived ethylene as a feedstock, has been successfully implemented.0.5mmol h− 1The rate of production of ethylene glycol. The preliminary techno-economic evaluation indicates the promising economic feasibility of the authors' ethylene glycol production process when powered by renewable electricity at currently achievable prices, providing references for methane oxidation, alcohol oxidation and epoxidation.
Informasi terkait
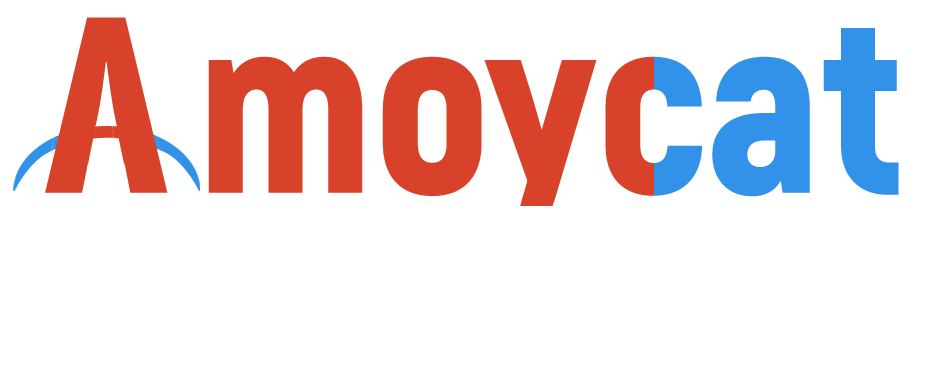
Hubungi kami
Situs web: Website
Alamat: No. 66 jalan selatan Xinyuan, distrik Haicang, Kota Xiamen, Provinsi Fujian, Tiongkok
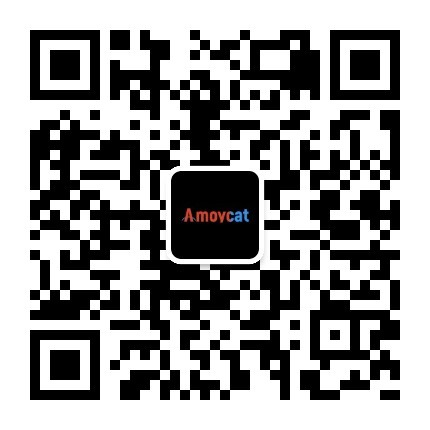
Kode QR akun resmi