Science: adipic acid, revolutionary breakthrough!
2024-08-02
Nylon is the first synthetic fiber in the world, which belongs to polyamide fiber (nylon). Its synthesis is not only a major breakthrough in the fiber synthesis industry, but also a very important milestone in polymer chemistry. Nylon can be seen everywhere in modern life, especially in the textile industry, we wear clothing, electrical equipment, mechanical equipment and other fields have nylon figure.
Nylon is the first synthetic fiber in the world, which belongs to polyamide fiber(nylon), its synthesis is not only a major breakthrough in the fiber synthesis industry, but also a very important milestone in polymer chemistry. Nylon can be seen everywhere in modern life, especially in the textile industry, we wear clothing, electrical equipment, mechanical equipment and other fields have nylon figure.
At present, nylon 66 is mainly used in the condensation process of hexamethylene diamine and adipic acid, and adipic acid is mainly produced by oxidizing cyclohexanone/cyclohexanol with nitric acid, with an annual output of millions of tons. However, this process requires the use of large amounts of corrosive strong acids and produces large amounts of NO, NO2,N2O and other gases, especially the greenhouse gas N2O, one of the main emission sources comes from the production process of adipic acid. In addition, adipic acid diesters are widely used in the production of plasticizers, perfumes, lubricants, solvents, active pharmaceutical ingredients, and nylon. The existing synthesis process of adipic acid has been mature as early as the 1940 s. In the past 80 years, scientists have been exploring new methods and new processes for the synthesis of adipic acid. On December 20, 2019,Albert, Germany-MatthiasBeller professors and collaborators at Einstein UniversityInScience published a paper and reported a new process for the production of adipic acid without nitric acid. They used a single-step palladium catalytic system to realize the one-step double carbonylation of butadiene to adipate. The catalytic system has high activity, High selectivity and versatility characteristics, solved the problems of the scientific and industrial circles for decades. Thomas Schaub of the University of Heidelberg-BASF Catalysis Research Laboratory wrote a review article and summarized the latest progress and prospects of adipic acid synthesis in recent years. (PS: I feel BASF is going to start on this patent soon, or has already done so)
FromTalking about the direct carbonylation of 1,3-butadiene
Carbonylation is one of the most important applications of industrial catalysis, producing more10 million metric tons of various carbonyl compounds (aldehydes, acids and esters). Although researchers first discovered the homogeneously catalyzed carbonylation process nearly 80 years ago, there are still several unachieved goals, the most significant of which may be the direct double carbonylation of 1,3-butadiene. The double carbonylation of butadiene will make it possible to produce adipate esters that are environmentally friendly, economical and efficient, and adipate esters are important monomers for the synthesis of polyamides and polyesters. The double carbonylation of butadiene to adipic acid and its esters may be a new alternative method to avoid the use of nitric acid and the greenhouse gas N2O emissions, and the selectivity of raw materials is more flexible. However, the selective double carbonylation of butadiene to produce adipic acid and its derivatives is also very difficult, because it requires two consecutive and non-selective carbonylation to obtain the target product with pentenoic acid as an intermediate. In earlier studies, the reaction was carried out in two steps, the carbonylation of butadiene to 3-glutaric acid, followed by the carbonylation of 3-glutaric acid to adipic acid using a homogeneous cobalt, palladium or rhodium catalyst. The conditions and catalysts for both steps need to be carefully selected because there are many potential unwanted by-products, such as isomers or polymers. Respectively optimized reactions are incompatible and cannot be developed into an efficient single-step reaction. For decades, many companies, including BASF, DuPont, Shell, Dow, Kulare and Sinopec, have been studying the feasibility of obtaining adipates through the dicarbonylation of butadiene. Although researchers have studied a variety of reaction systems in the laboratory, their industrialization process has faced problems of insufficient activity, insufficient selectivity, or both.
How hard is it?
In recent years, the method of double functionalization of butadiene to adipic acid has a new development.Mormul et al. reported rhodium-catalyzed dihydroformylation in the presence of ethanol to form an acetaldehyde-protected adipaldehyde intermediate, which can be oxidized to adipic acid. The total yield of butadiene-based adipic acid after oxidation is 52%. Although the double functionalization of the linear intermediate is achieved in the hydroformylation step, its economic feasibility is not high enough and needs to be further improved. Tortajada et al. recently reported the dicarboxylation of butadiene with carbon dioxide using a nickel catalyst. The reaction is carried out with unsaturated diacid as an intermediate, and then hydrogenated with the same catalyst, because it uses carbon dioxide as a raw material. At the same time, abundant metals are used as catalysts, but the yield of adipic acid is only 61%. The first step requires the addition of manganese as an auxiliary reagent, which hinders the application of the system in bulk chemical production. That is, the direct carbonylation of 1,3-butadiene provides a more economical and environmentally friendly route for the production of industrially important adipic acid derivatives. However, due to the complex reaction network of regioisomeric carbonylation and isomerization, no practical catalyst with high selectivity has been found.
new breakthrough
In view of this, Albert-Professor Matthias Beller et al. of Einstein University adopted the design of a pyridyl-substituted bidentate phosphine ligand, which, in coordination with palladium, catalyzes the formation of adipic acid diester from 1,3-butadiene, carbon monoxide and butanol. The yield of dialkyl adipic acid is ≥ 95%, the selectivity is 97%, and the atom economy is 100. This single-step catalytic system, as an alternative route for the synthesis of adipic acid and its esters, uses a palladium catalyst to add carbon monoxide to each end of butadiene without producing by-products, with high activity and selectivity. The catalyst can also be used to catalyze the conversion of 1,2-, 1,3-butadiene to a variety of other di-and tri-acid esters.
Key Points1. Reaction network for the synthesis of adipates from 1,3-butadiene
The selective double carbonylation of butadiene to adipoic acid and its derivatives requires two consecutive and non-selective carbonylations to reach the target product with pentenoic acid as intermediate. As shown in the figure below, there are several challenges to this catalytic process:(I) the catalyst must promote two different carbonylation reactions on the diene-based plate (which was previously unachievable);(ii) the linear dicarbonylation product must be selectively formed, although isomerization of the initially formed mono-carbonylated intermediate to the terminal olefin is thermodynamically particularly unfavorable;(iii) other side reactions such as telomerization, hydroalkoxylation and copolymerization must be suppressed.
Figure1 Reaction network for the synthesis of adipates from 1,3-butadiene
Key Points2. Ligand optimization of palladium-catalyzed 1,3-butadiene dicarbonylation
by using base-modifiedThe 1,2-bis [(di-tert-butylphosphino) methyl] benzene ligand (L1,dtbpx) derivatives were used to achieve selective dicarbonylation of 1,3-butadiene for the mass production of methyl methacrylate. The preliminary optimization study of the ligand showed that the activity of preparing linear dibutyl adipate 4a with p-toluenesulfonic acid as auxiliary catalyst was low at 120°C and 40 bar CO, but the selectivity was good. In order to improve the performance of the catalyst, dtbpx derivatives L2 and L3 were tested. However, no increase in activity was observed. Thus, the addition of a suitable base to this particular ligand backbone should increase the activity of the corresponding palladium catalytic system in alkoxycarbonylation reactions. In fact, the use of L4 greatly increases the activity and yield of the diester (77%), but at the expense of insufficient selectivity (48%). The ligand L5 (HeMaRaphos) was designed taking into account the appropriate reactivity of L4 and the appropriate selectivity of L1. The biscarbonylation of 1,3-butadiene was carried out in the presence of HeMaRaphos and Pd(II) trifluoroacetic acid [Pd(TFA)2] with a yield of 85% adipate diester and a linear selectivity of 97%.
Figure2 Palladium-catalyzed ligand optimization for 1,3-butadiene dicarbonylation
Key Points3. Palladium-catalyzed dichlorylation of 1,2-and 1,3-dienes
In order to understandHeMaRaphos the effect on the performance of the palladium catalyst, the team conducted kinetic monitoring experiments. In the first half hour, in Pd(TFA)2,Active palladium hydride formation was observed in an in situ mixture of L5 and p-toluenesulfonic acid (PTSA). Then, an alkoxycarbonylation reaction is carried out to selectively synthesize n-butyl n-butyl-3-enoate 3a. The intermediate accumulates continuously after 90 minutes, reaching about 50% of the maximum yield. At this time, the reaction is stopped and 3a can be separated from the reaction mixture. At the same time, the active catalyst also promotes olefin isomerization. The terminal olefin n-butylpent-4-enoate 3c was not detected due to its rapid conversion to linear adipate diester. Secondly, the effects of palladium precursor, acid, temperature and pressure are optimized in detail, which further improves the practicability of the process. The yield of the target product ester was 88-95% with a linear selectivity of 97%. For example, without additional solvent, the reaction can be carried out in the range of> 200-g with a Pd loading of only 0.05 mol%. In addition to the particular importance of the biscarbonylation of 1,3-butadiene in the chemical industry, this method also provides a solution for the price stabilization of other dienes in fine chemical production. To demonstrate the versatility of the catalyst system, the team used 15 different dienes and more than 30 alcohols to synthesize the corresponding diesters with high selectivity and yield. For example, several linear conjugated dienes 1a to 1f exhibit good reactivity and regioselectivity. Even for the internal conjugated double bond (1f), the isomerization reaction preferentially produces end products.
Figure3 Palladium-catalyzed dicarbonylation of 1,2-and 1,3-dienes
Future can be
This work proposes an economical and environmentally friendly alternative route for the preparation of adipic acid and its esters. The single-step palladium catalytic system is used for the double carbonylation of butadiene to adipate. The palladium catalyst adds carbon monoxide to each end of butadiene, has no by-products, and has high activity and selectivity. This strategy has great prospects for process applications, but before practical application, problems such as improving the long-term stability of the catalyst, finding a simpler and more effective ligand, the loading of the catalyst and the recovery of precious metals need to be solved.
References:
- Ji Yang, Jiawang Liu, HelfriedNeumann, Robert Franke, Ralf Jackstell, Matthias Beller. Direct synthesis ofadipic acid esters via palladium-catalyzed carbonylation of 1,3-dienes. Science,2019.DOI: 10.1126/science.aaz1293https://doi.org/10.1126/science.aaz1293
- Thomas Schaub. Producing adipic acidwithout the nitrous oxide. Science, 2019.DOI: 10.1126/science.aaz6459https://doi.org/10.1126/science.aaz6459
Artikel sebelumnya
Berikutnya
Informasi terkait
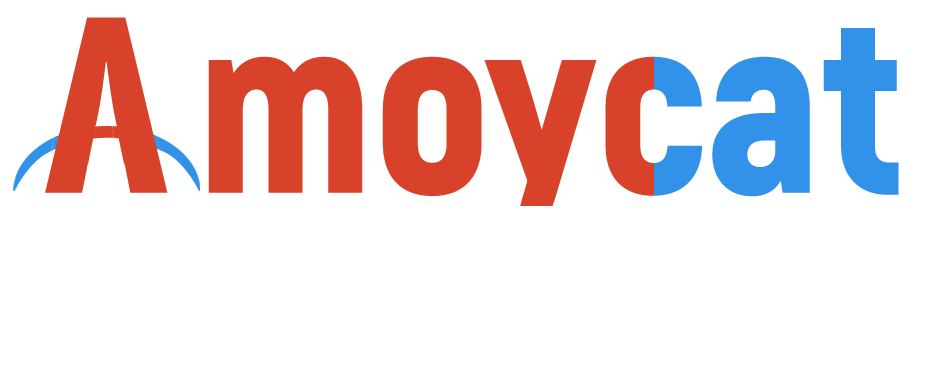
Hubungi kami
Situs web: Website
Alamat: No. 66 jalan selatan Xinyuan, distrik Haicang, Kota Xiamen, Provinsi Fujian, Tiongkok
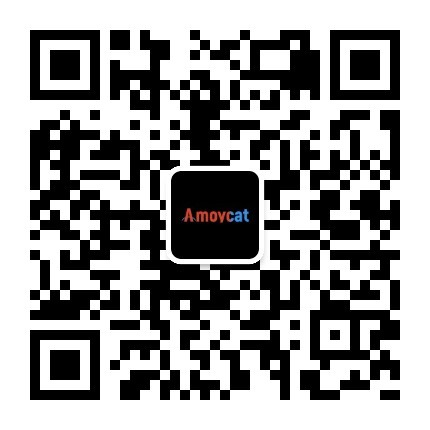
Kode QR akun resmi